Optimal delivers complete PAT software and hardware solution for continuous pharmaceutical production
Bristol, UK based Optimal Industrial Automation is just completing the design, construction and installation of a complete Process Analytical Technologies based control system, built to manage a pharmaceutical customer’s continuous manufacturing line, it delivers a huge increase in production efficiency, including regulatory compliance.
The new system builds on Optimal’s 26 years of systems integration experience in the pharmaceutical sector and makes use of the company’s latest synTQ® PAT Knowledge management software.
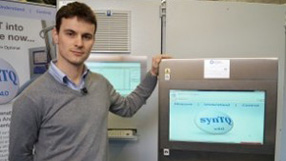
Even more significantly, some companies, like Optimal’s customer
Production-level PAT implementations can require considerable computing power, and Optimal’s latest is no exception. The system runs on no less than six high-powered
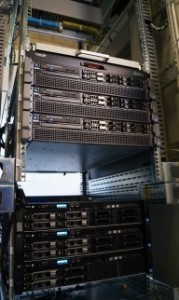
This data is processed and passed to a separate synTQ® server, which compares
Shop floor interactions with the system are made using three food-grade
Like all synTQ® applications, the new system has been built to be fully compliant with FDA guidelines on the traceability of manufacturing data. Complete records of the measurements taken during production, the configuration of the measurement equipment, the analysis models used and the process control parameters selected are retained within the system for audit purposes, or to facilitate
“The idea is that you design your PAT process and methods within synTQ® and then run the configured PAT system in real time when the process is operational. Each and every time you run that process, it uses exactly the same configuration, until you decide that you need to improve it. At which point, all those changes are audited and stored within the system,” explains Paul Gillham, Optimal’s technical lead on the project. “Everything is traceable, and furthermore synTQ’s
“Continuous production is an important goal for many pharma companies these days,” Concludes