About PAT
PAT Technology is the Future for Sectors Under Pressure to Deliver New Drugs Quickly, with Improved Quality & at Reduced Cost
Process Analytical Technology (PAT) is viewed by many in the pharmaceutical industry as expensive, extremely complex and too
In developing new process technologies, pharmaceutical manufacturers usually have a choice between achieving improved product quality,
The business benefits resulting from the implementation of PAT are
Case Studies
Summary of PAT Benefits for Business
Increased process understanding: at present, in some processes, there is a lack of process understanding: i.e. what are the
Reduced product variability: by achieving an understanding of the product and the associated process control, sources of variability can be identified and managed throughout the process and product lifecycle.
Reduced development and scale- up time: provided that PAT is applied early on in the development cycle, then, due to the increase in process understanding achieved, the time taken in development and scale-up can be greatly reduced.
Increase
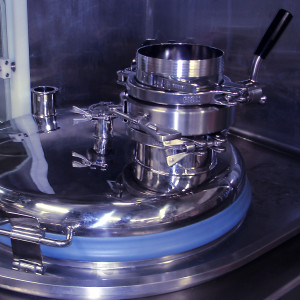
Extend the patent life of existing products: manufacturers of
Reduce production cycle times: by using
Reduced Work in Progress: the direct impact of reducing the cycle time is the reduction of Work in Progress. If a 10- fold reduction in cycle time is achieved, then a 10- fold reduction in Work in Progress is possible.
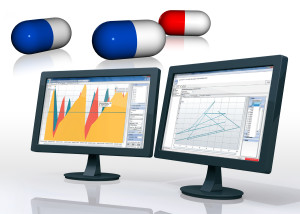
Use of alternative (less expensive) raw materials: due to the lack of process understanding, some manufacturing processes are limited to work with the raw materials upon which the process was initially validated. This means that the process cannot be used with raw materials from more
Reduce wastage during production: Some processes have in-built wastage due to inefficiencies and lack of process knowledge. These wastages can be designed in from the start and form part of the validation process. By using PAT, these wastages can be eliminated.
Prevent rejection of batches: as a result of processes run under PAT- based closed loop control, and with detailed process understanding, the manufacturing process is under control and rejected batches can, in the main, be eliminated.
Improvements in quality and consistency of quality: due to the process being under control, with Critical to Quality Attributes being continuously monitored and controlled throughout, process quality is inherent in the product. This leads to an overall improvement in quality, and consistency of that quality throughout.
Enable
Improve energy and material use: due to the process running more efficiently and with a shorter cycle time, energy usage is reduced.
Facilitate continuous processing: many processes using traditional control are constrained to the batch manufacturing process. However, once process understanding and a
i. Even further reductions in development and scale-up time as potentially there is no
ii. Even
iii. Even less staffing
iv. Even less energy consumption
v. Potentially add another method of protecting your patented product
vi. The manufacturing footprint becomes much smaller, and so manufacturing facilities can reduce in size.
vii. The potential for skid/
Release automation capabilities to improve the production process: using traditional methods, automation is restricted to controlling process parameters only. By implementing PAT, the true power of the automation system can be released, allowing it to control the whole process holistically, based on all the Critical to Quality Attributes.
Meet the new FDA Process Validation Guidance: the new FDA Process Validation Guidance (issued in 2011) effectively changes the validation paradigm from the 3- batch principal to a PAT controlled manufacturing method. Without implementing PAT, meeting the new guidance will be difficult, as it will demand much higher product sampling and testing regimes.
Reduce the cost of development, manufacturing and quality assurance: by implementing PAT, manufacturing costs will greatly reduce in virtually all areas, and this will make the manufacturing process much less expensive.
PAT Data Manager
All of the above benefits are dependent for their delivery upon a PAT Data Manager. Without the implementation of a regulatory- compliant PAT Data Manager, then a process cannot be truly monitored or controlled by PAT.
The functionality of a PAT Data Manager is basically to be the