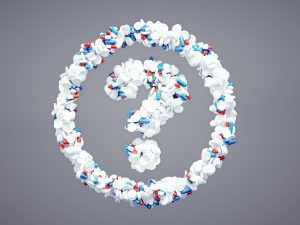
3d pharmaceutical question mark with included clipping path.
The role of a working structure based around PAT principles is to measure product quality attributes in real time, and ideally at every stage of a drug’s life cycle from initial development to full production. Measuring product quality in real time is key, and this is achieved non-destructively, typically by using a range of spectrometers in addition to univariate data sources, and making the quality predictions by pumping this live data into multivariate models. The end result is comprehensive product quality information and the ability to control the process based on quality.
Developing and introducing a fully capable PAT based development and / or production system can therefore appear daunting. Fortunately, it can be implemented in stages, one unit operation at a time, and a PAT Knowledge Manager such as synTQ® from Optimal Industrial Technologies can be grown as your deployment expands.
A PAT system can be deployed straight onto a production system; however, the largest overall time and financial gains can be made by deploying PAT early on in the product lifecycle – ideally at the R&D stage. If used from the early stage then the key chemometric models can be built in a GMP compliant way, and thus be available for use in a production environment. Furthermore, by developing these models and then the essential process understanding early on in the product’s life cycle, the scale-up times can be drastically reduced, and this has the potential for huge financial gains as it effectively increases the available patent life.
PAT processes generate huge amounts of data that must be turned into knowledge, so a PAT Knowledge Manager such as synTQ® is essential. This makes the myriad of interfaces and functions much more straightforward and manageable. It can interface to all data sources and consumers, provide a streamlined way of model building by integrating with your preferred MVA package, provide real time product quality live views in many forms to assist with the process understanding requirements, and in due course, provide a method for quality based process control.
In addition, a PAT system ideally needs to be configurable and not have to be programmed, as the configuration often needs to be achievable by users who are not software programmers. Yet further, it is extremely useful if functions such as the ability to run multiple models in the same “Orchestration” (PAT Method), be able to run virtual Orchestrations and be able to re-run historic data in new Orchestrations is possible, as these all help with productivity on the PAT development and process understanding journey.
The next step is to develop the control models for time and quality optimised production. These models can then be embedded in your PAT Knowledge Manager and run to either control your process directly, or (and more normally) used to alter the set points of your PLC or DCS system.
With your PAT system up and running on one unit operation, you are then really well placed to roll the technique out across the whole production process in an holistic manner, and then ultimately factory and companywide. But this can all start with a small deployment that would be used as a cost-effective stepping stone to better understand the demands and benefits of PAT. Ultimately, a PAT driven approach can open up the possibilities of continuous manufacturing with all the many benefits of such a process, plus the very real possibility of Real time Release of manufactured products.
Therefore, to conclude, there are many steps to be taken when adopting a PAT working structure, but they can be taken one at a time and the infrastructure grown as the deployments grow. Many key skill sets are also required, but by working with an experienced PAT company such as Optimal then the journey need not be as daunting as it first appeared.
Recent Comments