With the release of synTQ® V4.0, process industries such as life science, chemical, food plus oil and gas can now use one robust and proven software platform to develop, deploy and manage Process Analytical Technology (PAT) from the research laboratory to their global production networks. synTQ® V4.0 is the latest major update of the pioneering PAT implementation management software from Optimal Industrial Automation. synTQ® is in use today by six out of the top twelve global pharma companies, and by major industry regulators.
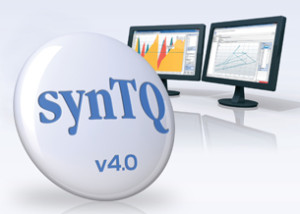
“synTQ® V4.0 has been created to meet two pressing – and often conflicting – challenges in a wide range of modern production processes,” says Optimal Technical Director, Dave Richards. “To gain a far greater degree of control over manufacturing processes, while managing an increasingly widely distributed production footprint.”
In its effort to drive up quality and reduce manufacturing costs, the global pharma industry is moving away from a reliance on end-of-line and end-of-process testing and inspection and towards on-line and in-line analysis and closed loop control, through the use of PAT. synTQ® supports this transformation by providing a bridge between the sophisticated instrumentation used to monitor manufacturing processes and the advanced multivariate analysis and modelling systems needed to interpret that data. At the same time, synTQ® records all of the measured and derived data, can feed the derived data into your control system of choice and does all of this in compliance with regulatory requirements.
Its new enterprise system architecture allows companies to manage all of their data from one central point, this greatly simplifying model management and enables the sharing of models between different synTQ nodes (no matter where in the world). Naturally, data archiving is also very much simplified. Such extended management and control capabilities are becoming increasingly critical as life science clients scale up and roll out their PAT systems. Using synTQ® 4.0, for example, companies can ensure that products manufactured at multiple sites across the globe all use the most up-to-date models and controls. The new capabilities are equally important as the use of external suppliers grows, allowing clients to integrate process monitoring and control at their contract manufacturing partners directly with their own quality control and recording systems.
The new synTQ® release includes significant enhancements for process users too. Enhanced data visualisation modules including web views further improve the system’s class-leading speed and usability, helping companies gather data and build, test and validate models faster and with more confidence.
These improvements, combined with synTQ’s real time analysis and control capabilities, give users a seamless route through PAT development, from initial laboratory tests and model design and validation, all the way to high-volume global production.
For companies just starting out on their PAT journeys, synTQ® is available in a range of different editions, offering tailored functionality at every stage in the development process, from small systems for initial investigative projects with single unit operations through to a plant wide distributed systems running multiple unit operations. Upgrading between versions is quick and painless, allowing users to invest only in what they need today, with the confidence that they can scale up smoothly when it suits them.
Recent Comments